Từ những chiếc bảng mạch điện tử thô sơ, cồng kềnh trong quá khứ, ngành sản xuất điện tử đã không ngừng phát triển. Để đáp ứng nhu cầu về các sản phẩm nhỏ gọn, đa chức năng, các nhà sản xuất đã tìm ra một giải pháp hiệu quả: công nghệ gắn kết bề mặt (SMT). SMT đã trở thành một công nghệ cốt lõi trong sản xuất điện tử hiện đại. Vậy, SMT là gì và tại sao nó lại quan trọng đến vậy?
Mục lục
1. Công nghệ SMT là gì?
Công nghệ SMT (Surface Mount Technology) là một phương pháp sản xuất linh kiện điện tử mà các linh kiện được gắn trực tiếp lên bề mặt bảng mạch in (PCB). Thay vì sử dụng dây dẫn để xuyên qua lỗ trên bảng mạch như công nghệ xuyên lỗ (THT), SMT tận dụng các linh kiện dán bề mặt (SMD- Surface Mount Device), được thiết kế với kích thước nhỏ gọn và không yêu cầu chân dài.
Công nghệ dán bề mặt (SMT) được ứng dụng rộng rãi trong điện tử tiêu dùng, ô tô, công nghiệp, y tế và quân sự, giúp giảm kích thước, chi phí và nâng cao hiệu suất. SMT tối ưu hóa thiết kế cho các thiết bị như màn hình LED, smartphone, máy móc công nghiệp, cảm biến y tế và hệ thống quân sự. Công nghệ này đảm bảo sản phẩm gọn nhẹ, bền bỉ và hoạt động chính xác.
Chú ý phân biệt SMT và SMD:
SMT (Surface Mount Technology) và SMD (Surface Mounted Device) thường bị nhầm lẫn, nhưng thực ra chúng có sự khác biệt rõ ràng về vai trò trong ngành công nghệ điện tử. SMT là một quy trình sản xuất, trong đó linh kiện được gắn trực tiếp lên bề mặt của bảng mạch (PCB) mà không cần khoan lỗ, giúp tiết kiệm không gian và tăng hiệu quả sản xuất. Công nghệ này sử dụng các máy móc tự động, chính xác để in keo, gắn linh kiện, và hàn chúng lại trên bề mặt mạch in. Trong khi đó, SMD là tên gọi của những linh kiện nhỏ gọn, được thiết kế để sử dụng trong quy trình SMT. Các linh kiện này không có chân dài như linh kiện trong công nghệ xuyên lỗ (THT), mà có chân ngắn hoặc không chân, phù hợp với việc gắn trực tiếp lên bề mặt bảng mạch.
Tóm lại, SMT là công nghệ và quy trình sản xuất, còn SMD là loại linh kiện được gắn lên mạch trong quy trình đó. Vì vậy, SMT và SMD không phải là hai khái niệm tách biệt mà thực sự là một cặp khái niệm bổ sung lẫn nhau. SMT là cách thức để gắn các linh kiện SMD vào bảng mạch, tạo ra các thiết bị điện tử nhỏ gọn, hiệu quả và tiết kiệm chi phí.
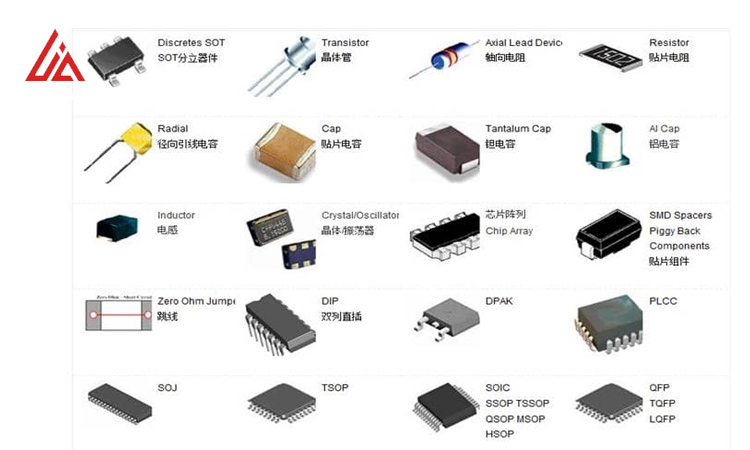
2. Các bước trong quy trình SMT
Quy trình SMT là một chuỗi các bước phức tạp nhưng được tối ưu hóa để đảm bảo tốc độ, chính xác và hiệu quả. Dưới đây là các bước cơ bản:
2.1. In keo hoặc hàn
Đây là bước đầu tiên trong quy trình SMT, nơi một lớp keo hoặc kem hàn được in lên các vị trí xác định trên bảng mạch.
Kem hàn (Solder Paste): Là hỗn hợp của bột thiếc và chất thông hàn (flux), giúp kết dính linh kiện với bảng mạch và đảm bảo dẫn điện tốt.
Quy trình in kem hàn:
- Sử dụng máy in stencil để phân phối kem hàn chính xác lên các pad hàn.
- Độ dày kem hàn thường dao động từ 0.12mm đến 0.15mm, tùy thuộc vào loại PCB và linh kiện.
Thông số quan trọng: Nhiệt độ bảo quản kem hàn thường là 0°C – 10°C, để tránh hiện tượng tách bột và thông hàn.
2.2. Gắn linh kiện
Máy gắn linh kiện tự động (Pick and Place Machine) là thiết bị thực hiện bước này.
Nguyên tắc hoạt động:
- Máy sẽ lấy linh kiện từ các cuộn băng (tape reel) hoặc khay (tray), sau đó định vị và đặt chúng chính xác lên vị trí có kem hàn trên bảng mạch.
- Tốc độ gắn có thể đạt tới 50.000 linh kiện/giờ với máy cao cấp.
Sai số định vị: Độ chính xác của máy thường ở mức ±0.01mm, đảm bảo khả năng xử lý các linh kiện nhỏ như chip 0201 (kích thước 0.6mm x 0.3mm).
2.3. Hàn nóng chảy
Sau khi linh kiện được đặt lên bảng mạch, bảng mạch sẽ được đưa vào lò hàn nhiệt để kem hàn nóng chảy và kết dính linh kiện vào PCB.
Quá trình hàn nóng chảy:
- Reflow Soldering là kỹ thuật phổ biến nhất, sử dụng khí nóng để làm nóng bảng mạch qua các vùng nhiệt độ khác nhau.
- Nhiệt độ đỉnh (peak temperature) trong lò hàn thường từ 240°C – 250°C đối với hợp kim thiếc-bạc-đồng (SAC305).
Cảnh báo: Nếu nhiệt độ không được kiểm soát chính xác, các lỗi như hàn lạnh, bong bóng hàn hoặc linh kiện bị trượt có thể xảy ra.
2.4. Kiểm tra và sửa lỗi
Bước cuối cùng là đảm bảo chất lượng của sản phẩm thông qua các công đoạn kiểm tra tự động và sửa chữa.
Kiểm tra tự động (AOI – Automated Optical Inspection):
- Máy AOI sử dụng camera và thuật toán để quét toàn bộ bảng mạch, phát hiện các lỗi như sai vị trí linh kiện, thiếu hàn, hoặc ngắn mạch.
- Độ chính xác của AOI có thể đạt tới 98% trong phát hiện lỗi hình học.
Kiểm tra X-ray:
- Dùng cho các bảng mạch phức tạp hoặc linh kiện BGA, nơi các chân hàn nằm ẩn bên dưới.
Sửa lỗi thủ công: Nếu phát hiện lỗi, bảng mạch sẽ được chuyển đến kỹ thuật viên để khắc phục, thường thông qua hàn tay hoặc rework station.
3. Ưu điểm của công nghệ SMT
Công nghệ SMT đã trở thành tiêu chuẩn trong ngành sản xuất điện tử nhờ những lợi ích vượt trội về hiệu suất, chi phí và tính linh hoạt. Dưới đây là phân tích chi tiết về từng ưu điểm của SMT:
3.1. Tăng hiệu suất sản xuất
Tự động hóa quy trình:
SMT sử dụng các máy móc hiện đại như máy in stencil, máy gắn linh kiện (Pick and Place Machine), và lò hàn reflow, giúp tối ưu hóa tốc độ sản xuất.
Tốc độ gắn linh kiện có thể đạt tới 50.000 – 70.000 linh kiện/giờ, nhanh hơn nhiều so với kỹ thuật hàn thủ công hoặc xuyên lỗ.
Giảm thời gian lắp ráp:
Quy trình SMT được tích hợp hoàn toàn tự động, từ in kem hàn đến kiểm tra lỗi, giúp giảm đáng kể thời gian chu kỳ sản xuất (cycle time).
Với dây chuyền sản xuất SMT, một bảng mạch PCB trung bình chỉ cần từ 2 – 5 phút để hoàn thành.
Năng suất cao hơn:
SMT cho phép gắn nhiều linh kiện nhỏ trên một diện tích nhỏ, giúp tăng mật độ linh kiện lên gấp 1.5 – 2 lần so với công nghệ xuyên lỗ (THT).
3.2. Giảm kích thước sản phẩm
Linh kiện nhỏ gọn:
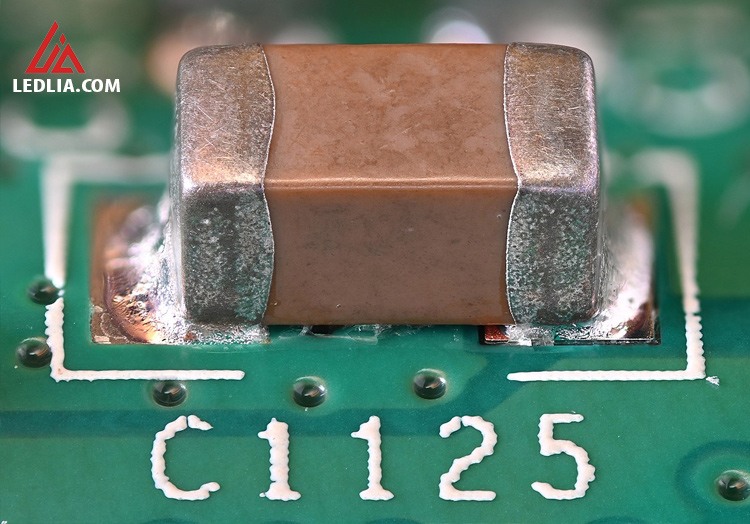
Các linh kiện SMD (Surface Mount Devices) như điện trở 0201 (0.6mm x 0.3mm) và tụ 0402 (1mm x 0.5mm) có kích thước nhỏ hơn đáng kể so với các linh kiện xuyên lỗ truyền thống.
Nhờ thiết kế tối giản này, bảng mạch và thiết bị điện tử ngày càng nhỏ gọn, phù hợp với xu hướng phát triển sản phẩm hiện đại như điện thoại thông minh, đồng hồ thông minh, và máy tính bảng.
Tăng mật độ linh kiện:
SMT cho phép đặt linh kiện ở cả hai mặt của bảng mạch, giúp tối ưu hóa không gian.
Một bảng mạch SMT có thể chứa số lượng linh kiện gấp đôi so với bảng mạch THT cùng kích thước.
Sản phẩm mỏng hơn:
SMT loại bỏ nhu cầu về chân linh kiện dài, giúp giảm độ dày của sản phẩm điện tử, mang lại tính thẩm mỹ cao và dễ dàng tích hợp.
3.3. Tối ưu hóa chi phí sản xuất
Tiết kiệm nguyên vật liệu:
Không cần khoan lỗ trên PCB, SMT giúp tiết kiệm vật liệu và công đoạn, đồng thời giảm chi phí sản xuất PCB.
Kem hàn sử dụng trong SMT có khả năng tái chế cao hơn, giúp giảm lãng phí vật liệu.
Tự động hóa giảm chi phí nhân công:
SMT sử dụng dây chuyền tự động hóa, giảm đáng kể nhu cầu về lao động thủ công.
Theo nghiên cứu, chi phí nhân công cho sản xuất SMT giảm tới 30% – 40% so với công nghệ xuyên lỗ.
Giảm tỷ lệ lỗi:
Với độ chính xác của máy móc, tỷ lệ lỗi hàn và lắp ráp trong SMT giảm xuống chỉ còn 0.1% – 0.3%, giúp giảm chi phí sửa chữa và bảo hành.
3.4. Cải thiện độ chính xác và độ tin cậy
Độ chính xác cao:
Máy gắn linh kiện SMT có độ chính xác đến ±0.01mm, đảm bảo các linh kiện nhỏ nhất cũng được đặt đúng vị trí.
Công nghệ kiểm tra AOI (Automated Optical Inspection) giúp phát hiện lỗi chính xác lên tới 98%.
Độ tin cậy của sản phẩm:
Mối hàn SMT có diện tích tiếp xúc rộng hơn, giúp kết nối chắc chắn và giảm khả năng bị hở mạch trong điều kiện rung lắc hoặc nhiệt độ thay đổi.
Linh kiện SMD được thiết kế để chịu đựng tốt hơn các yếu tố môi trường như nhiệt độ cao, độ ẩm và bụi bẩn.
Giảm nhiễu điện từ (EMI):
SMT giảm chiều dài đường dẫn điện trên PCB, làm giảm độ tự cảm (inductance) và khả năng phát sinh nhiễu điện từ, giúp sản phẩm hoạt động ổn định hơn.